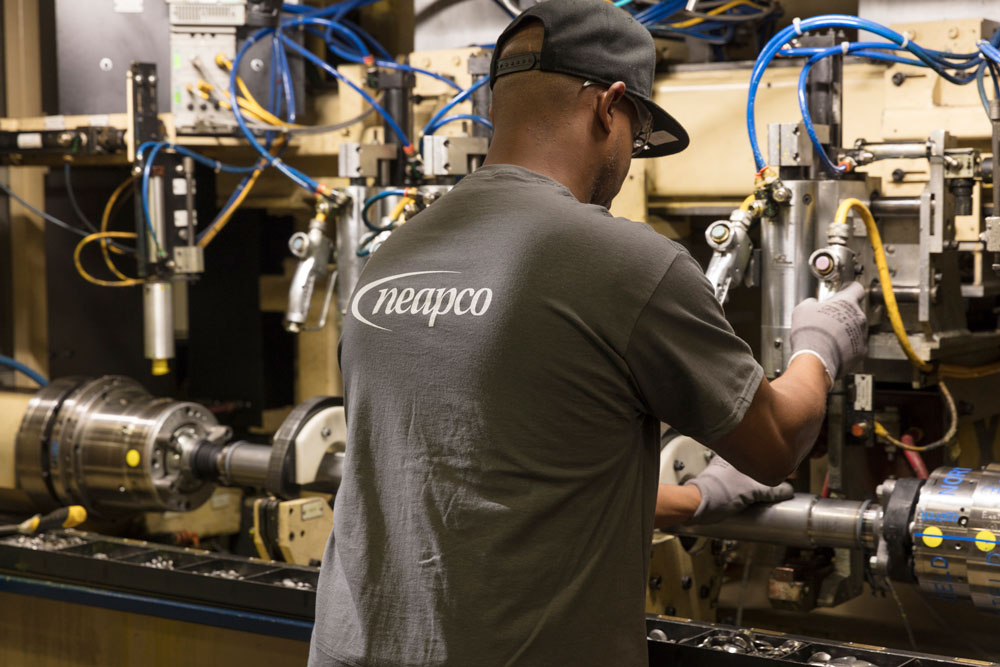
NEWS

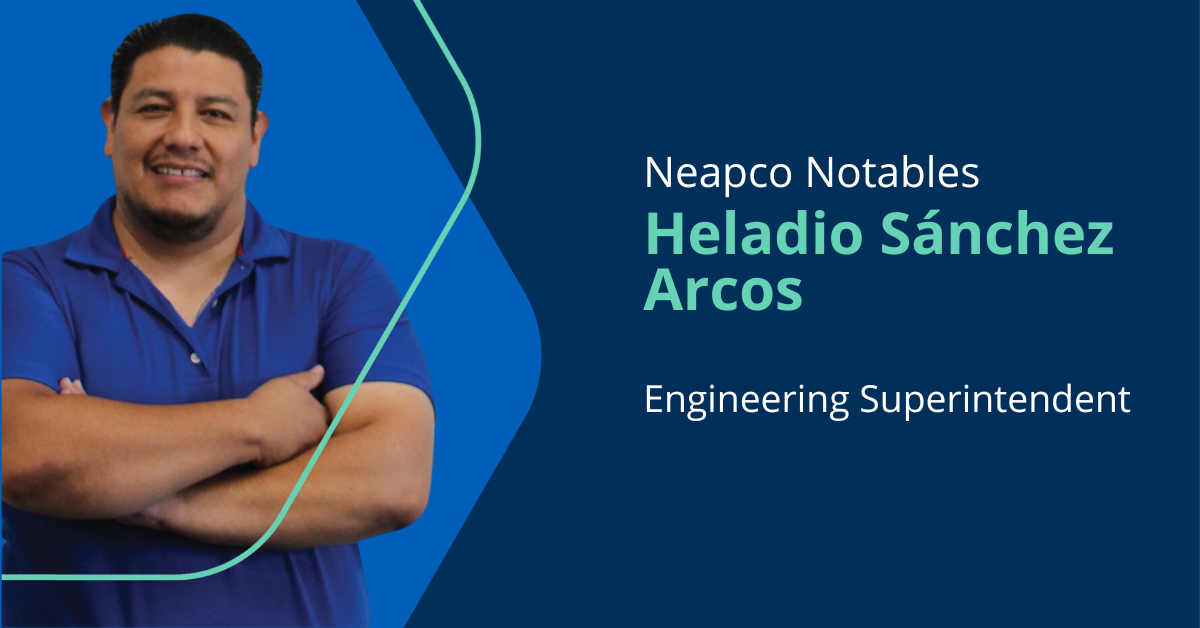
11.14.2024
Neapco Notables | Heladio Sanchez Arcos, Engineering Superintendent Drive Shaft/Assembly Half Shaft
Neapco’s global success is driven by our exceptional people. It all starts with the supportive and dynamic learning environment fostered by our dedicated and passionate team members, making every day at work enjoyable.
In this edition of Neapco Notables, we highlight Heladio Sanchez Arcos, Engineering Superintendent Drive Shaft/Assembly Halfshaft at Neapco’s Saltillo, Mexico plant. Over the years, Heladio’s role has evolved significantly, particularly as he transitioned from production and quality roles into the engineering space. He has embraced new challenges like learning Friction Welding, which was unfamiliar to him before joining the company.
Heladio shares insights into his role at Neapco, his passion for problem-solving, and why he believes continuously seeking improvements is essential to success.
Tell us a bit about yourself and what brought you to Neapco. What made your new role at Neapco more challenging than your previous experiences?
I’m from Veracruz, Mexico, and I hold a bachelor’s degree in Mechatronics Engineering. With 17 years of experience in the automotive industry, I’ve worked across a variety of production, quality, and engineering roles. I joined Neapco in November 2021 because I was drawn to the challenge of learning new processes, particularly in Friction Welding and Balancing, which are key processes in producing propshafts. Although I had experience in Laser Welding, Friction Welding was new territory for me, making this role both exciting and challenging.
Can you tell us more about your role at Neapco? In addition, are you involved in any of Neapco’s internal programs or initiatives?
Currently, I serve as the Engineering Superintendent in the Drive Shaft Business Unit, where my focus is on optimizing machining and assembly processes. I also support new program launches and oversee engineering changes.
Having transitioned from a production and quality role into engineering, I’ve really come to appreciate the innovation and problem-solving aspects of this field. I enjoy the constant pursuit of improvements—whether it’s saving the company money, making tasks easier for operators, or integrating new technologies to reduce costs.
My daily responsibilities include coordinating with my team to reduce scrap, minimize downtime, enhance quality performance, implement safety improvements, manage engineering changes, and support new projects. It’s a collaborative effort, and I’m fortunate to work with such a skilled and dedicated group.
I’m also actively involved in the Water Sustainability Program at Neapco, where I participate in efforts to reduce water consumption and improve the quality of water disposal. I believe sustainability initiatives like this are not only vital for the environment but also reflect our company’s commitment to social responsibility. I’ve been involved with the program since its inception, and it’s been rewarding to see how our efforts contribute to a larger goal of environmental stewardship.
What’s the most important lesson you’ve learned while working at Neapco and why is this significant to you?
One of the most important lessons I’ve learned at Neapco is the value of perseverance in seeking process improvements. This is crucial because there’s always more than one way to approach a problem, and sometimes the best solutions come from exploring all possible options. I often think of Thomas Alva Edison, who made hundreds of attempts before successfully inventing the lightbulb.
A prime example of innovation at Neapco was the implementation of a Snap Ring Expander in our GM assembly line. When I started, I noticed that operators were using traditional methods like a hammer and chisel to expand Snap Rings. These tools had been in use since the program’s inception, and while they had served the team well, I saw an opportunity to enhance the process. After learning that the previous modernization efforts had faced challenges, we successfully introduced the Snap Ring Expander to improve efficiency and streamline workflow.
Determined to find a better solution, Edgar Martinez and I worked with a local supplier to develop a new tooling concept and after several trials, we successfully eliminated the need for the hammer and chisel. This improvement reduced headcount on the assembly line, minimized ergonomic and safety risks, improved first-time-through rates, and cut downtime. The innovation has resulted in significant cost savings at Neapco Saltillo, and our Belleville plant is considering implementing the same solution.
What do you enjoy most about working at Neapco and are there any upcoming projects you are particularly excited about?
I enjoy the teamwork and the sense of accomplishment that comes from achieving results. My team is made up of highly skilled and dedicated professionals who are deeply knowledgeable about the processes we manage. We consistently meet our key performance indicators (KPIs), and this year we were honored to receive a Supplier Quality Award from GM. Additionally, we successfully passed external audits with zero findings, which is a testament to our commitment to excellence.
I’m excited about taking on responsibility for the assembly lines in the Halfshaft Business Unit, which is a new and exciting challenge for my career. This role will involve managing additional assembly lines and working with more customers across the automotive industry. The scope and complexity of these projects will require close attention to detail, and I’m looking forward to working with new technologies and strategies to support our customers.
What are some of your favorite things to do outside of work?
I love spending time with my family. We enjoy traveling, swimming, hiking, and discovering new places together. It’s important to me to balance work with quality time with my family, and I always look forward to our adventure.
Interested in joining the Neapco team? Click here to take a look at our open positions.